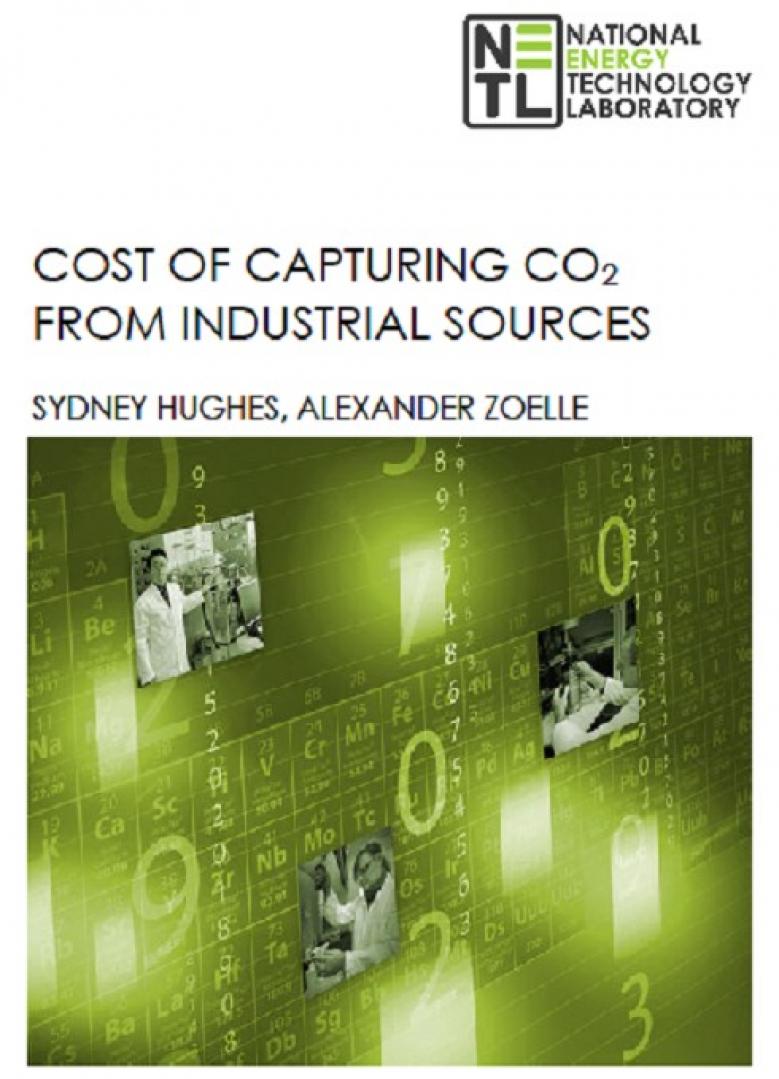
NETL's Cost of Capturing CO2 from Industrial Sources and Industrial Carbon Capture Retrofit Database
With the proliferation of initiatives and commitments to dramatically reduce greenhouse gas emissions, several common industrial processes have been identified as potential opportunities for decarbonization, due to their relatively high CO2 effluent concentrations and inability to avoid the emissions through process change. The National Energy Technology Laboratory’s study titled Cost of Capturing CO2 from Industrial Sources evaluates nine representative industrial facilities (ammonia, ethanol, ethylene oxide, natural gas processing, coal-to-liquids, gas-to-liquids, refinery hydrogen, cement, and iron/steel) —each with CO2 emission concentrations above that found in the flue gas streams of coal-fueled power plants (~11-16 percent) —to estimate the levelized cost of CO2 capture. The cost of capture in each case considers the equipment required for state-of-the-art solvent-based CO2 capture, where applicable, along with compression, dehydration, and balance of plant equipment, such as that required for heating, cooling, and power supply. For industrial sources with very high CO2 concentrations (nearly 100 percent CO2), CO2 capture may only require compression and dehydration. Sensitivity analyses consider the cost implications associated with changes to financial assumptions and plant size (i.e., the amount of CO2 available for capture) for each case. For most cases, greenfield costs (i.e., the additional cost that would be associated with including capture in a greenfield plant build) and retrofit cost implications are both considered.
The cost and performance estimate methodologies and data from the study were used to create a public Microsoft Excel tool—the Industrial Carbon Capture Retrofit Database—that allows users to estimate the cost of CO2 capture at existing ammonia, ethanol, cement, natural gas processing, and hydrogen production facilities. The tool provides screening level estimates—additional study (e.g., a FEED study) considering the unique circumstances and requirements present at a specific facility is necessary to reduce uncertainty in support of prudent investment decisions.